Resources for Improved Manufacturing Operations
The manufacturing sector has always been a cornerstone of economic growth, and as technology evolves, so too must manufacturing operations. To maintain a competitive edge and meet the demands of modern markets, manufacturers need to explore and integrate new resources and strategies. These may range from automation and advanced software solutions to the implementation of smart technologies like the Internet of Things (IoT). Keep reading to learn how these interventions can herald a marked improvement in manufacturing efficacy and output.
Streamlining Supply Chain Management With Advanced Software Solutions
Effective supply chain management is pivotal for any manufacturing operation. Advanced software solutions provide a means to track, control, and optimize the flow of goods from raw materials to finished products. By harnessing these tools, manufacturers can drastically reduce lead times and improve their response to supply chain disruptions.
One such tool is enterprise resource planning software, which integrates all facets of an operation from inventory management to customer relations. This type of software provides a singular view of the entire business process, enabling more informed decision-making and strategic planning.
Enhanced visibility across the supply chain through software also facilitates better communication with suppliers and customers. Real-time updates and predictive analytics help in anticipating needs and managing resources more effectively, avoiding overstocking or stock-outs.
The Role of IoT and Big Data in Enhancing Production Efficiency
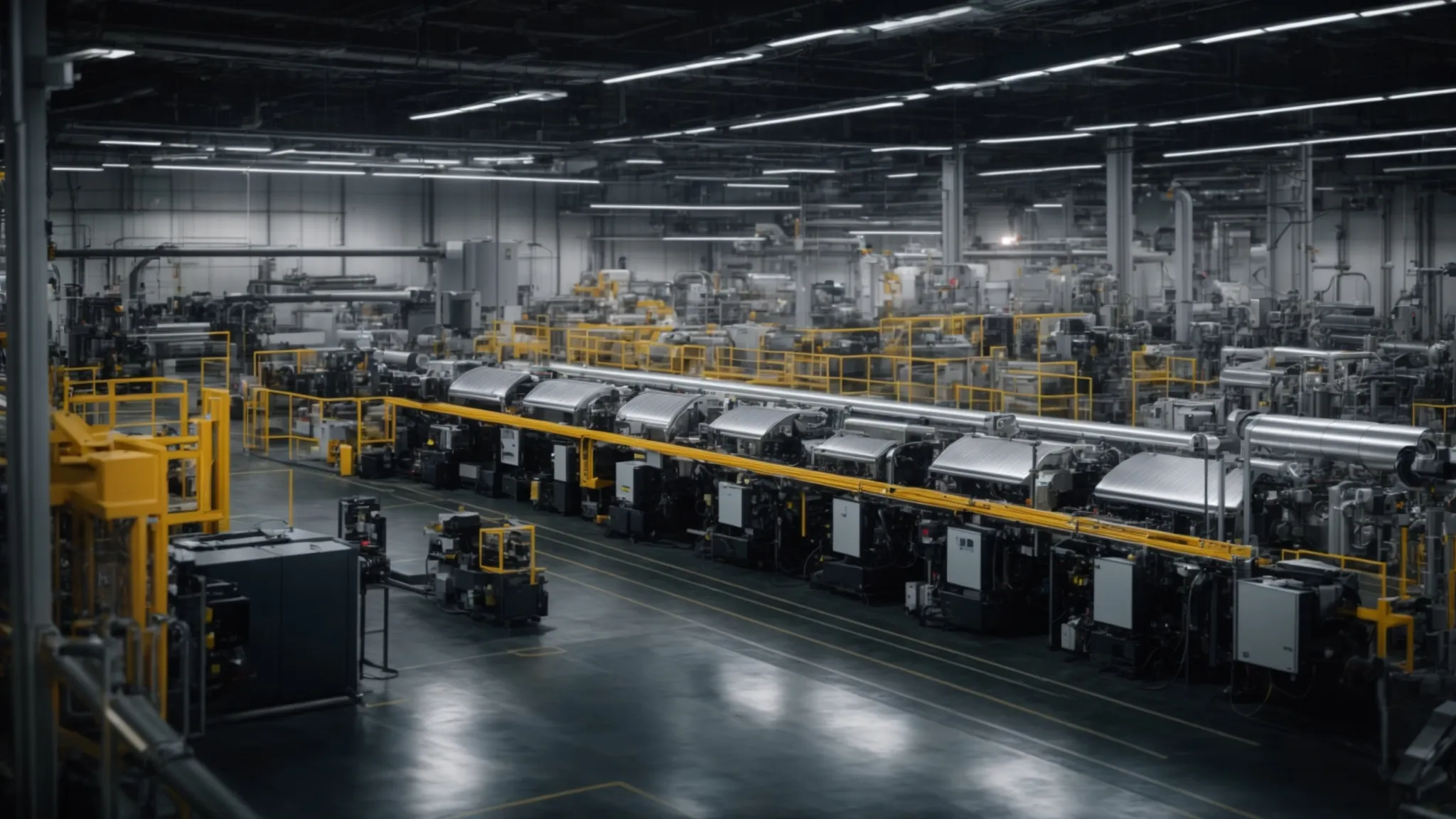
The IoT and big data analytics are creating new opportunities for manufacturers to optimize production lines. IoT devices collect vast amounts of data in real time from various points in the manufacturing process, offering a level of insight that was previously unattainable. Utilizing tools such as OTTO Seo AI can further enhance these initiatives, giving businesses the edge they need to succeed in the competitive landscape of modern manufacturing.
By analyzing this big data, manufacturers can pinpoint inefficiencies and predict potential machine failures before they occur. This proactive approach to maintenance reduces downtime and extends the lifespan of equipment. The integration of IoT allows for a more adaptive production system that can react to issues instantaneously.
Moreover, big data analytics can inform product development, leading to better designs that consider customer feedback and usage patterns. These insights can drive innovation and help manufacturers stay ahead of trends. As the manufacturing environment becomes more complex, the ability to sift through large volumes of data quickly is becoming essential to maintain competitiveness.
Implementing Lean Manufacturing Principles for Operational Excellence
Lean manufacturing principles are centered around maximizing value while minimizing waste. Implementing these principles can lead to significant enhancements in efficiency and quality. By focusing on value from the customer’s perspective, manufacturers can streamline processes to produce products using fewer resources.
Key to the success of lean manufacturing is the concept of continuous improvement. This involves regularly evaluating and adjusting operations to find incremental ways to enhance performance. Engaging all employees in this process promotes a culture of excellence and creative problem-solving.
Visual management tools and techniques such as value stream mapping help identify and eliminate inefficiencies, revealing areas within operations that contribute to waste or do not add value. Lean practices often result in a more organized workplace that significantly reduces operational costs and improves workflow.
Investing in Employee Training Programs for Skilled Workforce Development
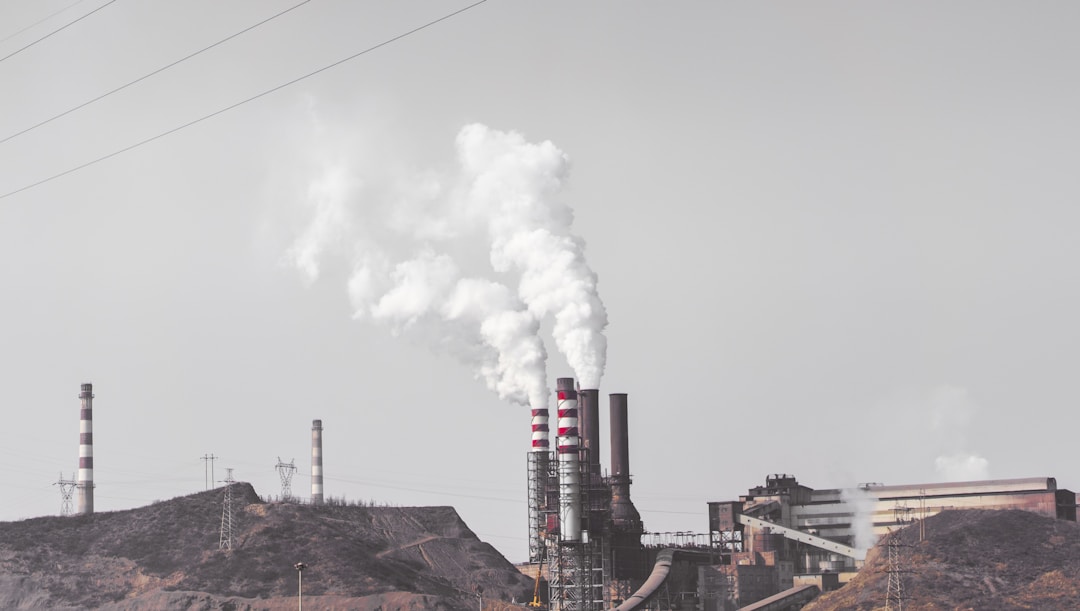
A well-trained workforce is key to leveraging the full potential of new manufacturing technologies and processes. Investing in employee training programs ensures that staff are capable of operating new systems effectively and adapting to shifting industry demands.
Training programs can cover a wide range of skills, from technical know-how in operating advanced machinery to software proficiencies and problem-solving abilities. By prioritizing skill development, companies can create a flexible and versatile workforce.
Moreover, continuous learning and development initiatives can significantly enhance employee retention. Workers are more likely to remain loyal to employers who invest in their growth and provide opportunities for career advancement.
Altogether, incorporating advanced technologies and lean manufacturing principles, while investing in employee training, lays a roadmap for improved manufacturing operations.